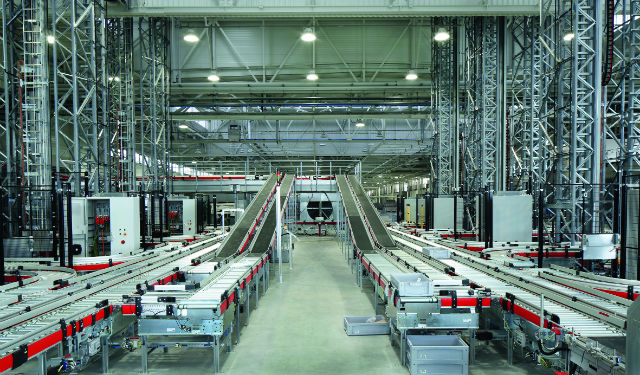
L’Industrie 4.0 est déjà une réalité en Franceet ne se limite plus aux grandes entreprises de l’automobile ou de l’agroalimentaire. L’industrie électrique et électronique a déjà commencé son évolution (sa révolution ?) pour passer à l’Industrie du Futur afin d’optimiser, de personnaliser et de sécuriser sa production. Cette révolution va nécessiter la maîtrise de nouveaux outils et techniques, l’implication et la formation du personnel, la gestion et la sécurisation des données. Aujourd’hui, les résultats sont déjà là pour de grands groupes, mais aussi des PME et ETI et devraient participer à la redynamisation du tissu industriel français et accroître la valeur ajoutée industrielle par une plus grande compétitivité.
La formalisation du concept d’Industrie du Futur sous l’intitulé « Industrie 4.0 » est née en Allemagne au début des années 2010. Ce concept s’est rapidement développé en France, même si son niveau d’appropriation, de mise en œuvre et de résultat est encore inférieur à celui de nos voisins Allemands. Cette industrie 4.0 fait référence à une quatrième révolution industrielle que nous vivons et qui devrait aboutir à une usine ou à un atelier du futur plus agile et flexible, plus, respectueux de ses employés et de l’environnement grâce à une intégration numérique de l’ensemble de la chaîne d’approvisionnement et de production.
Cette usine devient numérique et flexible par une communication continue entre les différents outils et postes de travail avec l’utilisation de capteurs communicants. Des outils de simulation et de traitement des données recueillies sur toute la chaîne de production permettent de produire une réplique virtuelle de cette chaîne, de générer des simulations de test, de permettre aux techniciens de se familiariser avec un nouvel outil de travail, de nouvelles procédures complexes ou même de réparer une machine ou préparer une maintenance.
Selon Laurent Siegfried, délégué du secteur Industrie du Gimélec, « cela va permettre une réduction du délai de mise sur le marché, une prise de décision et une autonomie sur la chaîne. Mais surtout, un gain en qualité, avec des capteurs permettant une maintenance prédictive et une plus grande réactivité en cas de panne grâce à la réalité virtuelle. La sécurité et la qualité de vie de l’opérateur de la machine sont augmentées par exemple grâce à l’utilisation d’une tablette virtuelle qui permet de voir ce qui se passe à l’intérieur de l’armoire de contrôle ».
Le résultat sera une usine économe en énergie et en matière première grâce à une coordination des besoins et des disponibilités. « Il faut une logistique 4.0 pour une Industrie 4.0. »
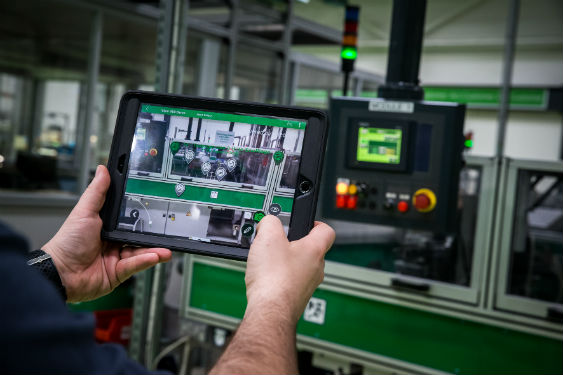
(c) Schneider Electric
De nouvelles technologies à mettre en œuvre
Le passage à l’usine du futur ne se réduit pas simplement à la mise en œuvre de nouvelles technologies ou d’innovations, mais celles-ci vont se retrouver et se combiner dans les nouveaux processus de fabrication ou maintenance. On peut lister :
• L’Internet industriel des Objets (IIoT) : à partir de capteurs, placés sur les machines ou les pièces en cours de fabrication, les données relevées sont distribuées sur un réseau à tous les maillons de la chaîne de fabrication (automates, logiciels de supervision, système informatique de l’entreprise).
• Smart Data : à partir de la masse de données stockées qu’il faut traiter et analyser, la chaîne de production sera optimisée. « Dans l’industrie, on ne fait pas du Big Data, mais du Smart Data. Et le Smart Data, c’est capter la bonne donnée, la transformer (ou la contextualiser) et s’en servir pour optimiser son procédé de fabrication », indique Serge Catherineau, directeur marketing Industrie du Futur de Schneider Electric.
• Le Cloud : les données et ressources de toute la chaîne industrielle sont hébergées sur une infrastructure centralisée et mutualisée. Mais des données peuvent être traitées localement (Edge Computing) pour éviter un transfert de données trop important et réduire le temps de latence.
• La réalité augmentée pour assister l’opérateur de production, aider à la maintenance ou pour la formation des personnels, l’objectif étant « l’opérateur augmenté ».
• La fabrication additive (ou impression 3D) est utilisée pour le prototypage, mais aussi la fabrication de pièces, avec de nouvelles approches de conception ou une optimisation de la matière.
• La robotisation, avec des robots collaboratifs (ou « cobots ») qui assistent l’opérateur humain en automatisant certaines de ses tâches dans un espace de travail partagé. Pour Serge Catherineau, « cela remet l’opérateur au centre de l’usine, avec cet “opérateur augmenté” qui obéit au cerveau de l’opérateur et fait les tâches à faible valeur ajoutée. Mais il reste le réglage qualité pour l’opérateur sur la machine ».
• Le jumeau numérique donne une représentation numérique de l’outil de fabrication. « Cela permet de simuler et de valider des machines, de tester des processus sans passer par l’étape “prototype”, de repérer et corriger très vite les erreurs d’ingénierie », selon Thierry de Vanssay, directeur de région Digital Industry de Siemens.
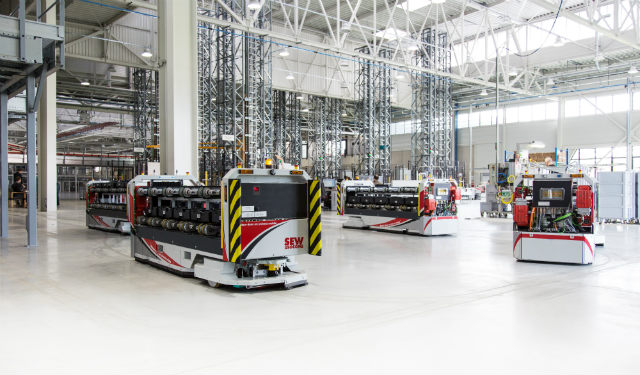
Des plateformes comme outil de gestion, d’optimisation et d’aide à la décision
Pour tirer profit de ce Smart Data, ces données collectées en permanence par ces objets connectés et capteurs, les spécialistes proposent des plateformes Cloud de plus en plus performantes et pouvant s’adapter à tous les secteurs d’activité et toutes les entreprises.
ABB a développé ABB AbilityTM, une plateforme de technologies de l’Internet industriel et une infrastructure Cloud (Microsoft Azure pour son environnement ultra-communicant). « Cette offre inclut plus de 220 applications, selon Eric Dubois, Digital Business Developer d’ABB France. Elle devient un écosystème digitalindustriel ouvert, accessible à l’échelle mondiale pour nos clients, partenaires et fournisseurs. ABB AbilityTM associe une expertise approfondie du domaine d’activité et une expérience inégalée en matière de connectivité. Elle permet à nos clients de savoir plus, d’agir plus et d’agir mieux, ensemble, en leur faisant partager :
– des connaissances approfondies dans plus de 20 secteurs industriels ;
– plus de 40 ans d’expérience en matière de technologies digitales ;
– un leadership mondial en termes de connaissance de l’automation et des Process industriels ;
– une position de leader dans les systèmes de contrôle commande et l’automation industrielle. »
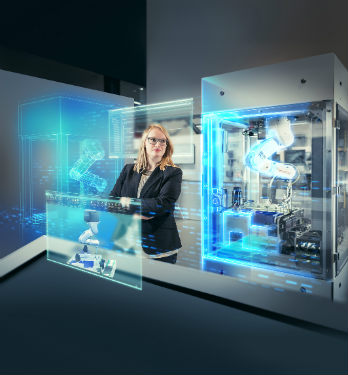
Siemens propose MindSphere, une plateforme Cloud évolutive, prête à l’emploi afin de collecter et utiliser les données. Thierry de Vanssay explique : « MindSphere permet de consolider, stocker et partager l’information issue de différents sites et de la traiter avec des outils analytiques allant jusqu’à l’intelligence artificielle. » Siemens s’est associé à Atos qui met en œuvre et enrichit cette offre avec ses propres solutions à valeur ajoutée : services d’intégration ou d’infrastructures de sécurité pour des applications spécifiques à chaque client.
Schneider Electric a déployé sa plateforme EcoStruxure sur plus de 480 000 sites dans le monde ; une plateforme système ouverte, interopérable et compatible IoT. Pour Serge Catherineau, « EcoStruxure, c’est aussi la capacité de conseiller le client et tout le consulting qui va avec pour repenser la méthodologie et transformer les usages. L’objectif étant de migrer d’une hiérarchie de contrôle classique vers une topologie des actifs d’usine et vers une architecture axée sur ces actifs. »
De son côté, Rockwell Automation s’est associé à PTC, leader de l’IoT et de la réalité augmentée, pour proposer une solution intégrée d’information qui permette d’accroître la productivité, d’optimiser l’efficacité des usines et améliorer l’interopérabilité des systèmes de leurs clients.
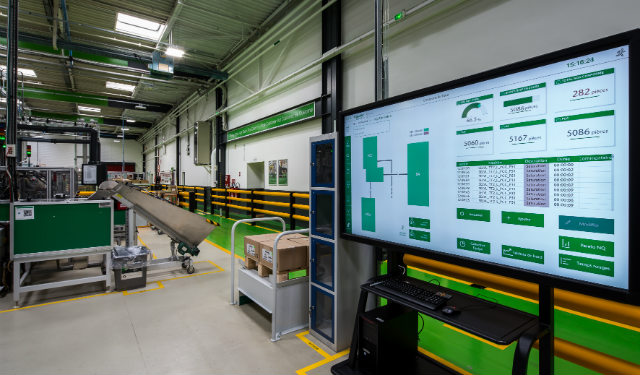
L’offre de General Electric se base sur sa plateforme Internet industriel Predix. Cette plateforme Cloud PaaS (Platform as a service) permet de développer des applications d’Internet des Objets industriels, de collecter et analyser les données générées par les machines. Predix est basée sur une technologie open source « Cloud Foundry ». La plateforme regroupe également des outils de Data Management et de Data Science.
Des constructeurs comme Wago Contact proposent aussi des solutions associées à leurs gammes d’automates programmables. Ainsi, explique Pascal Tigréat, responsable du département Automation de Wago Contact : « avec notre gamme d’automates PFC, nous remplissons toutes les exigences d’interopérabilité et de cybersécurité avec plus de 24 protocoles avec ouverture sur le Cloud d’Amazon Web Services, Microsoft Azure ou IBM Bluemix et sur un Cloud Wago pour héberger les données. Pour nos clients, nous essayons de rendre simples des solutions assez complexes et loin de leurs préoccupations premières : faire fonctionner leur usine ou leurs machines. »
La maintenance devient prédictive ou prévisionnelle
Selon Serge Catherineau, « le 2e pilier de l’industrie du futur est la disponibilité : comment faire pour que les machines ne tombent pas en panne et produisent avec plus de qualité. On est dans la performance des équipements et il faut passer de la maintenance programmée qui coûte cher avec un impact faible (-18 % de pannes) à la maintenance prédictive par une analyse du fonctionnement de la machine (détecter une dérive). Il faut alors agir pour maintenir, changer un sous-ensemble sans pénaliser la production pendant un temps “rouge” ou un changement de série, par exemple. C’est l’axe n° 1 pour éviter la panne en mode crise. »
Cette maintenance prédictive se fera donc par une approche analytique basée sur les données grâce aux capteurs intégrés de façon cohérente aux endroits sensibles et l’intelligence artificielle, avec un « machine learning » au service de la maintenance. Une bonne mise en œuvre de cette maintenance 4.0 nécessitera une vision globale de l’entreprise, une architecture de réseau solide pour traiter toutes les données au profit de la maintenance et une organisation fonctionnelle de cette maintenance. Ainsi, le fabricant de moteurs d’avions Rolls Royce utilise une plateforme de reconnaissance de pannes développée grâce aux outils et services de Microsoft Azure pour détecter un problème avant déclaration de panne et décider de changer une pièce défaillante.
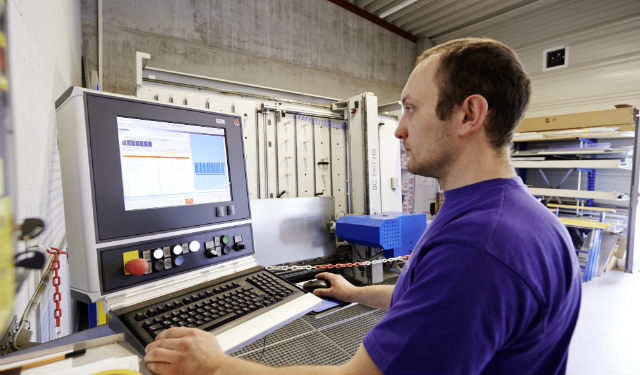
Penser « cybersécurité » pour protéger le savoir-faire et les installations
Serge Catherineau le rappelle : « La sécurité ne doit pas être dégradée : sécurité des biens, des équipements, des personnes et de l’entreprise. C’est la priorité n° 1 du patron. »
Cette digitalisation des usines, des process, va générer de nouveaux risques avec des millions de machines et de capteurs qui échangent des informations dans le monde entier. Autant de cibles potentielles d’attaques par des virus ou des logiciels malveillants, de vols de données stratégiques (conception, ingénierie) ou de pertes de données. Tous ces problèmes pouvant entraîner des arrêts de production ou des incidents graves.
Pour Delphine Legendre, chargée de projets Marketing de Phoenix Contact France, « nous proposons des solutions de routeurs de sécurité mGuard générant une communication chiffrée en sortie pour différentes configurations de réseau public ou privé et d’accès à distance pour les machines ». Chez Siemens, la solution « Industrial Anomaly Detection » permet d’identifier les incidents liés à la sécurité, tels que des intrusions non autorisées et des logiciels malveillants, et de prendre les contre-mesures. Cette solution permet d’identifier les vulnérabilités sur les appareils et de suivre leur comportement en matière de communication. Ce système de détection d’anomalie s’appuie également sur l’intelligence artificielle selon un mécanisme d’apprentissage. On pourra, pour plus d’informations, se reporter aux guides et publications de l’ANSSI (Agence nationale de la sécurité des systèmes d’information).
Qu’est-ce que cela implique en termes de formation et de changements organisationnels ?
Les spécialistes de l’Industrie 4.0 parlent de collaboration de plusieurs technologies, souvent nouvelles, et de la collaboration de l’homme et de la machine. Pour que cette révolution ne se fasse pas au détriment des salariés, il faut que la maîtrise des données et des nouveaux outils soit accessible à tous dans l’entreprise et pas seulement aux data scientists ou aux experts de l’IT ; des experts qui, selon Serge Catherineau, sont souvent difficiles à trouver, mais ne manquent pas de propositions d’embauche. On parle alors de « datalphabétisation » des salariés. Ces besoins de formation et d’évolution des compétences vont toucher aussi bien les ingénieurs, les ingénieurs des méthodes, les techniciens de maintenance ou de bureaux d’études, mais aussi les opérateurs qui devront apprendre à travailler avec leur « cobot » ou réparer une machine grâce à la réalité augmentée. Donc pour Olivier Vallée, responsable du programme Usine du Futur de Rockwell Automation : « un tel chantier impose une transformation organisationnelle qui touche aux fonctions et aux compétences des salariés, les métiers vont évoluer, de nouveaux métiers vont arriver. Il faudra beaucoup communiquer en interne ». Il y a un déplacement du rôle des managers vers beaucoup plus de transversalité.
Il reste encore des freins à cette migration vers l’industrie du futur, mais les mises en œuvre réussies sont nombreuses
Si les grands groupes de l’automobile, de l’aéronautique ou de l’agroalimentaire sont passés ou vont transformer leurs usines au 4.0, ce n’est pas encore le cas des PME/ETI.
Pour Laurent Siegfried, c’est le cas « pour des PME adossées à un grand client ou limitées à des machines spéciales et qui n’en ressentent pas le besoin. Celles-ci, il faut les accompagner pour gagner des marchés à l’export. Pour elles, il faut montrer que l’on peut passer au 4.0 pas à pas à partir d’un logiciel ou d’un premier investissement ». L’accompagnement des PME n’est pas parfait avec quelquefois des offres concurrentes, mais les actions de l’AIF (Alliance pour l’industrie du futur), du Gimélec, des CCI ou des pôles de compétitivité sont nombreuses. Le Cetim est aussi un acteur important dans ce domaine.
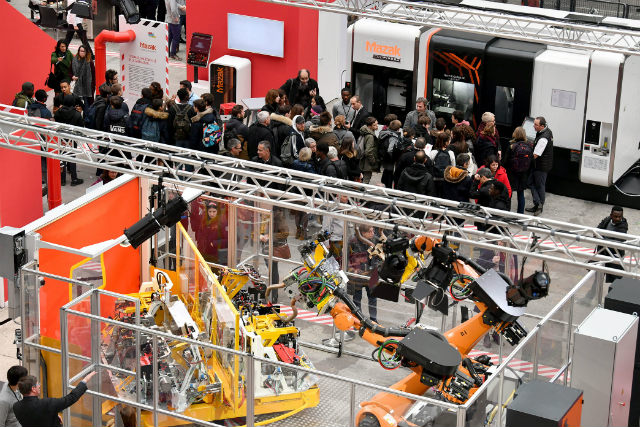
Et pour montrer ce que sera l’industrie de demain, rien de tel que des manifestations ouvertes à tous comme « L’Usine Extraordinaire » au Grand Palais, en plein cœur de Paris en octobre dernier : un parcours immersif mêlant lignes de production en fonctionnement et rencontres avec des ingénieurs et opérateurs de machines.
Mais pour montrer que l’on peut faire entrer dans l’industrie du futur des sites nouveaux ou anciens en production, quoi de mieux que la visite de quelques sites. Ainsi, Schneider Electric propose à des clients de visiter son usine du Vaudreuil, dans l’Eure. Ce site ancien produisant des contacteurs et variateurs de vitesse est le premier en Europe de 100 sites pilotes sur lesquels sont déployées les meilleures solutions techniques digitales du groupe : Internet des objets pour la maintenance prédictive, robotique collaborative pour les tâches répétitives, véhicules à guidage automatique pour l’approvisionnement des chaînes, modélisation dans le Cloud de grandeurs physiques sur la chaîne, gestion intégrée du bâtiment pour modéliser et faire des économies d’énergie. Cette transformation s’est faite avec une formation interne des collaborateurs grâce à de nouvelles technologies (vidéos, réalité augmentée). Ce site a été labellisé en 2018 « Vitrine Industrie du Futur » par l’AIF.
C’est une usine nouvelle de 11 500 m2 produisant 4 500 moteurs et motoréducteurs par jour que SEW-Usocome a implantée à Brumath en Alsace, une usine labellisée « Usine du Futur ». Le concept de l’usine 4.0 de SEW-Usocome est d’assurer une synchronisation des flux physiques et des flux d’informations depuis l’enregistrement de la commande jusqu’à la livraison, avec une traçabilité complète des produits tout au long de la chaîne de valeur. Ceci grâce à des solutions de transitique et de robotique basées sur les produits et solutions du groupe. Avec un double objectif : augmenter la productivité et améliorer le confort des salariés.
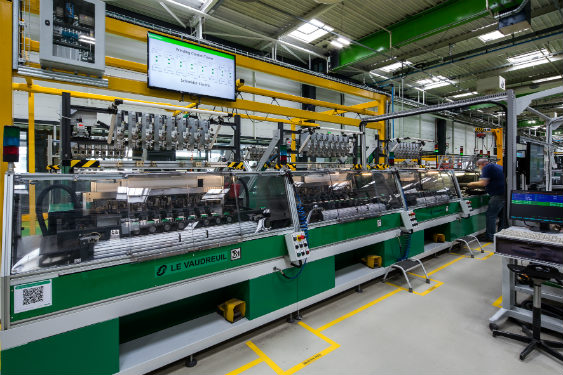
La fabrication des coffrets et tableaux électriques, souvent assurée par des PME/ET, passe aussi à une production numérique 4.0. Pour Pierre-André Stadler, chef de Produits électriques de Rittal SAS, « les solutions proposées aux tableautiers, quelle que soit leur taille, vont de la conception à une fabrication entièrement digitalisée depuis le plan numérisé et le jumeau numérique de l’armoire jusqu’à l’ingénierie et la logistique, en passant par la découpe laser 3D et l’assemblage. Même les petits tableautiers tiennent à ces solutions qui permettent une optimisation de tout le processus de travail, une forte réduction des délais de fabrication et une meilleure réactivité aux demandes des clients ».
Jean-Paul Beaudet