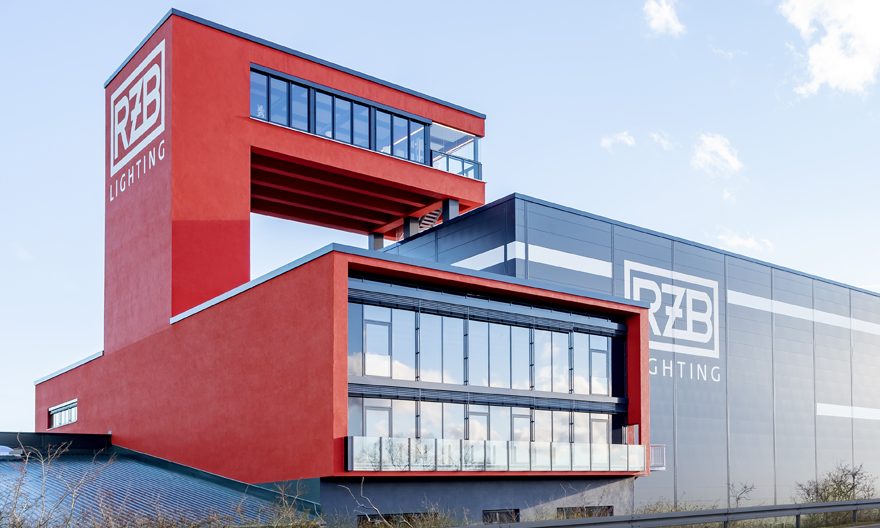
RZB (Rudolf Zimmermann, Bamberg) est une entreprise familiale allemande créée il y a plus de 80 ans à Bamberg, au nord de la Bavière. Le groupe compte deux marques, Sonlux, spécialisée dans l’éclairage mobile de chantier, et RZB dans l’éclairage technique intérieur et extérieur. L’entreprise dispose de deux sites de production en Allemagne, à Sondershausen pour Sonlux et pour l’injection plastique du groupe, et à Bamberg, siège historique de la marque, pour les produits RZB et le travail du métal et montage.
Installé depuis 1950 dans la zone portuaire de la ville, au bord du canal Rhin-Main-Danube, le site de production RZB de Bamberg s’étale sur 100 000 m² et compte 600 employés. Pascal Rinckenberger, directeur commercial du groupe RZB et Stéphane Vanel, directeur commercial RZB France, détaillent le processus de production des luminaires et présentent l’usine de Bamberg, fleuron industriel du groupe.
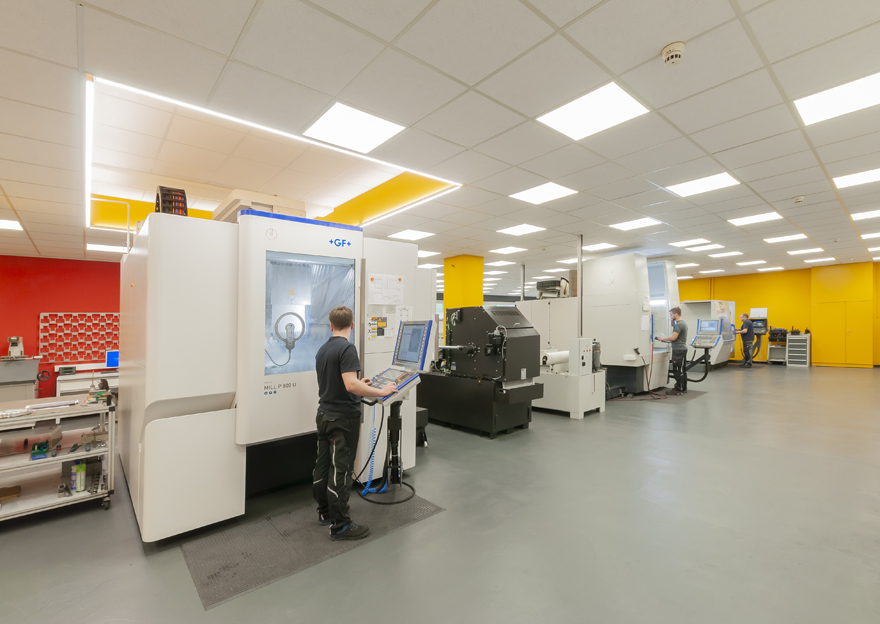
Fabrication de l’outillage
« Nous sommes propriétaires de notre propre outillage, ce qui nous permet de proposer des produits exclusifs à nos clients. »
RZB conçoit et fabrique ses produits de A à Z sur le site de Bamberg. Pour façonner les pièces nécessaires à la réalisation de ses luminaires, l’atelier de fabrication de l’outillage réalise les
moules pour l’injection plastique, ou des formes de découpe et des éléments de presse pour le travail du métal. 32 employés assurent la fabrication de ces outillages, qui sont ensuite destinés à la production des pièces métalliques ou plastiques.
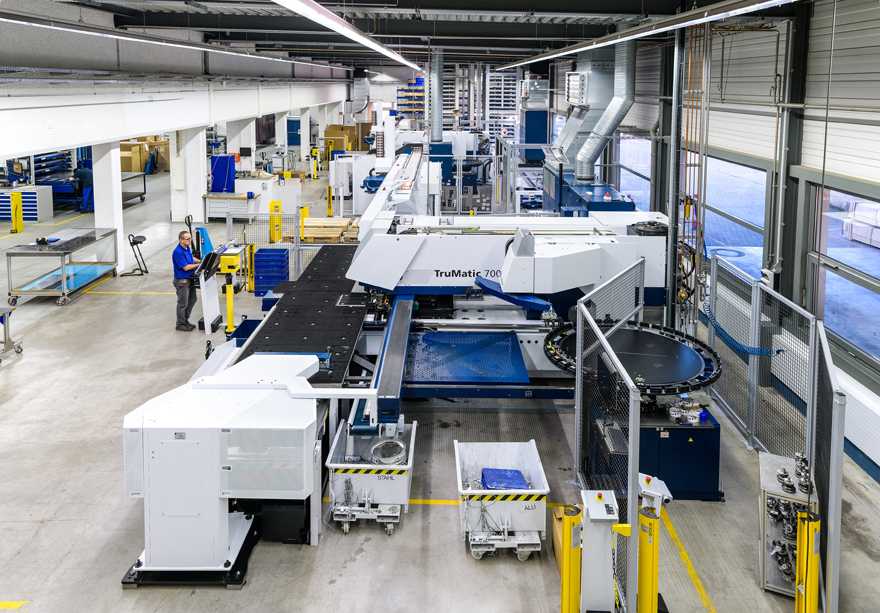
Production des pièces métalliques
« Nous disposons de trois lignes Trumpf entièrement automatisées pour fabriquer les pièces métalliques destinées à la fabrication des luminaires. »
Lors de la phase de production, les outillages sont utilisés pour découper les plaques métalliques, qui sont acheminées automatiquement dans la presse depuis le magasin. La machine effectue la découpe laser et le poinçonnage. Les profils en aluminium, nécessaires à la fabrication des luminaires linéaires, des mâts ou des borniers sont découpés à partir de tubes massifs, dans un hall séparé. L’ensemble de la tôlerie est réalisé en interne. Une fois les pièces découpées, poinçonnées ou extrudées, elles sont récupérées par des opérateurs et envoyées à l’atelier de peinture.
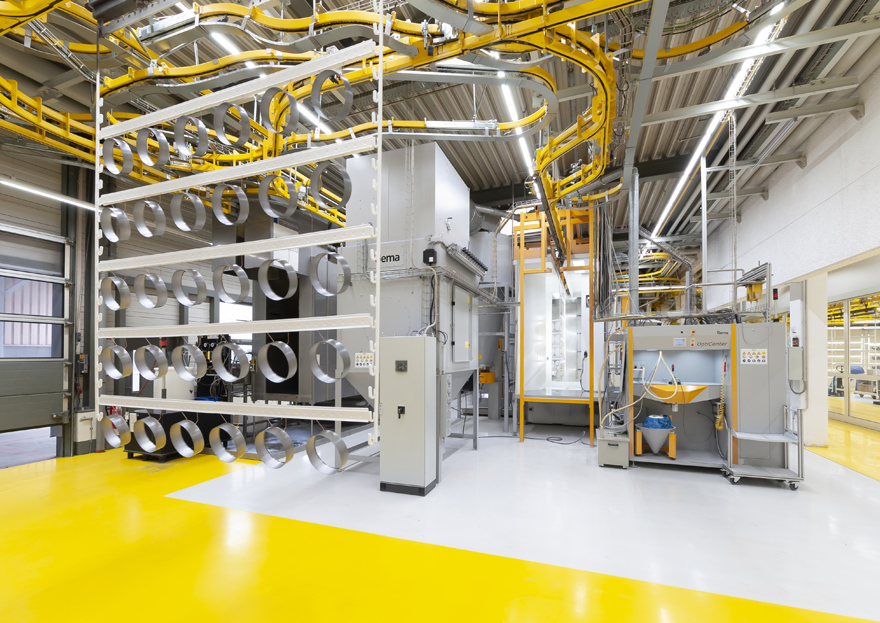
Peinture
« Nous possédons des machines très flexibles qui nous permettent un changement de couleur en deux heures et le processus est, là aussi, entièrement automatisé. »
Les pièces fabriquées à l’atelier de préparation du métal arrivent à l’atelier de peinture qui compte une vingtaine d’opérateurs. Elles passent dans un bain pour supprimer les impuretés, puis sont séchées avant d’être pulvérisées avec de la poudre de peinture et cuites. RZB a investi il y a cinq ans dans une machine automatisée, à haute efficacité énergétique, capable de tourner 24 h/24. L’ensemble des luminaires de la marque sont proposés de manière standard en trois couleurs : blanc, anthracite et gris. La flexibilité de la machine permet de changer de couleur en deux heures et de réaliser des séries spécifiques sur demande. Les petites séries sont peintes dans des cabines indépendantes. Une fois peintes, les pièces se dirigent vers le montage.
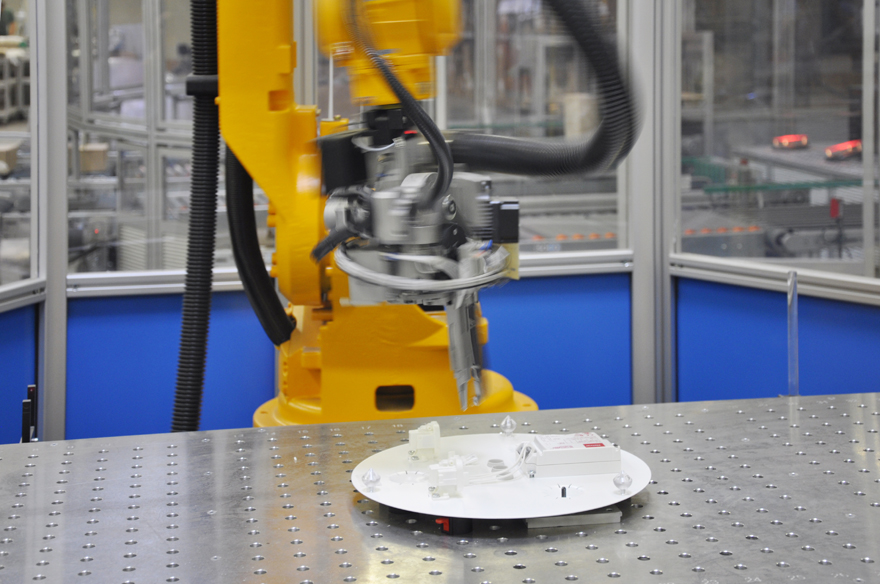
Montage
« Le processus de câblage est effectué par un robot, ce qui nous permet d’atteindre 100 % de qualité. »
RZB dispose de trois robots de câblage. Il suffit de saisir la référence produit et de visser l’alimentation et les modules LED sur la plaque électronique pour que le robot assure le câblage. L’atelier montage emploie 125 personnes, dont certaines réalisent un montage sur table, en intégrant les différents composants, avant l’intervention du robot. Les grandes séries sont entièrement automatisées, les moyennes peuvent être câblées à l’aide du robot, mais les petites séries sont câblées manuellement. Une fois les produits câblés, les employés ajoutent les pièces de carrosserie et réalisent le packaging, en intégrant les instructions de montage. Avant leur sortie de l’atelier, 100% des luminaires sont testés. Ils sont maintenant prêts à être expédiés.

Un site à haute performance environnementale
« Grâce à des panneaux photovoltaïques sur le toit, un système de récupération de chaleur, un passage au 100 % LED et le suivi des indicateurs des Nations unies, le site respecte de nombreux critères environnementaux. »
Sur les 60 000 m² de toiture que compte le bâtiment, la moitié est couverte de panneaux photovoltaïques, qui fournissent 30 % de la consommation d’électricité du site. De plus, un système autonome de récupération de chaleur a été intégré au plus près des fours de l’atelier de peinture, pour chauffer l’usine et les bureaux, combiné à un nouveau système de chauffage à haut rendement. Le site bénéficie d’une certification ISO 9 001 de management de la qualité et a mis en place les 17 indicateurs pour le suivi des objectifs de développement durable (ODD) des Nations unies.
Rubrique réalisée par Alexandre Arène
RZB Lighting
Rheinstraße 16
96052 Bamberg – Allemagne